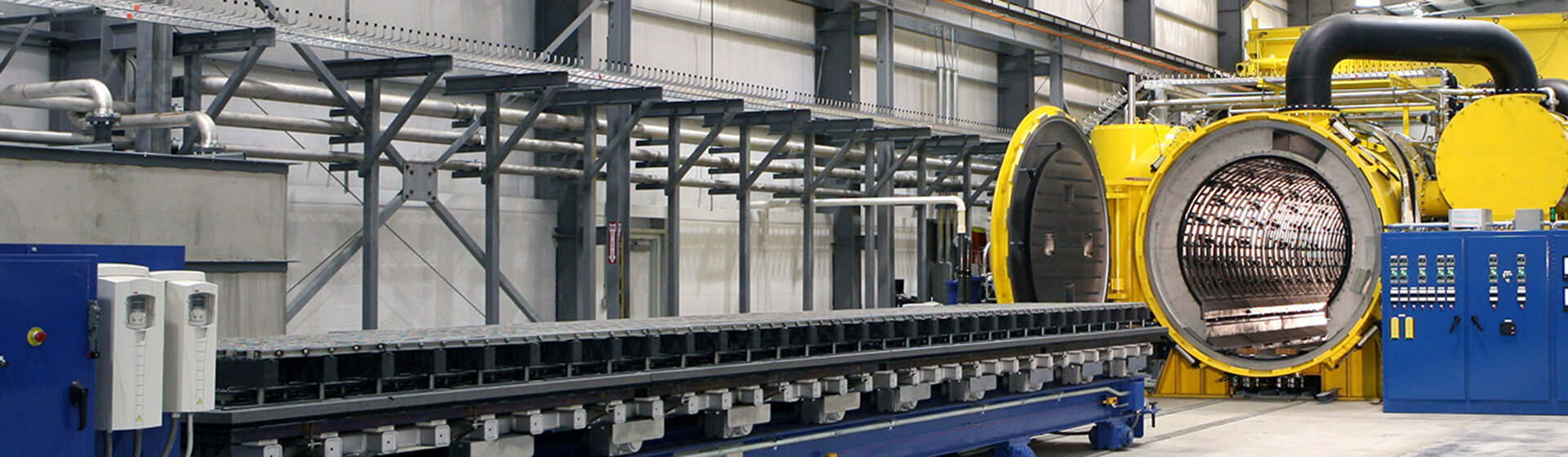
Horizontal Car Bottom Loading Vacuum Furnaces
Horizontal Car Bottom Loading Vacuum Furnaces
The HCB-2EQ Model is a horizontal, car bottom, vacuum heat treating furnace specifically designed for large, heavy workloads. It is a high temperature, high vacuum, batch furnace with electric resistance heating elements mounted both in the circular hot zone and the full length of the car bottoms. Designed for heat treating, hardening, brazing, stress relieving, normalizing, annealing, tempering, sintering, homogenizing, degassing, diffusion bonding, creep forming.
Features and Benefits
- Front and rear hinged autoclave locking-ring doors for loading / unloading from both ends of the furnace.
- The front and rear transfer cars provide smooth safe, powered loading / unloading of large heavy loads of parts. By utilizing both ends of the furnace for loading, parts can be staged during processing, eliminating downtime between furnace cycles
- Uniformity of ±10°F throughout hot zone
- Available in either graphite or metallic hot zones
- Dual or triple* high performance, external gas quenching systems provide high velocity, 2 bar cooling of large workloads (*depending on overall length of furnace vessel; offered as options)
- Multiple pumping systems provide for operating vacuum in 1×10-5 Torr
- Fully automated and programmable SolarVac®industrial controls package
- Designed for long life, easy maintenance, minimal downtime, and low cost of operation
Hot Zone
Solar Manufacturing produces both metallic shielded or graphite insulated hot zones, depending on your specific processing requirements.
Graphite Hot Zone Construction:
- Operating temperature: 2400°F
- Maximum temperature: 2500°F
- Temperature uniformity: ±10°F
- AMS 2750 compliant
- Survey temp points at 1000°F / 1500°F / 2100°F
- Insulation: multiple layers of 1/2” thick high purity rayon graphite felt
- Hot Face: one layer of 0.070” thick CFC, or other materials upon request
- Heating Elements: rugged segmented, curved graphite bands or ML Molybdenum bands, supported with a Solar proprietary design to reduce metallization of insulation materials and increasing the ease of maintenance
- Hearth: Machined graphite rails supported by molybdenum hearth posts
- Support Structure: insulation and heating elements are mounted on a heavy duty 304 stainless steel fabrication with heavy duty, back up shields of 0.090” thick
All-Metal Shielded Hot Zone Construction:
- Operating temperature: 2400°F
- Maximum temperature: 2500°F
- Temperature uniformity: ±10°F
- AMS 2750 compliant
- Survey temp points at 1000°F / 1500°F / 2100°F
- Insulation: combinations of molybdenum and/or stainless steel sheet metal
*Other shielding materials are available depending on the application and temperature requirements
- Hot Face: Lanthanated Molybdenum hot face increases hot zone life expectancy
- Heating Elements: rugged segmented, curved graphite bands or ML Molybdenum bands, supported with a Solar proprietary design to reduce metallization of insulation materials and increasing the ease of maintenance
- Hearth: TZM hearth rails for strength at high temperatures
Power Supply
The power supply is adequately sized to properly and efficiently heat the furnace and workload.
- MSI SCR fan cooled or air conditioned NEMA cabinet
- Hunterdon VRT (water cooled)
Vacuum Chamber
- Available in either carbon steel or stainless steel construction
- Door closure methods includes pneumatically actuated autoclave locking rings on both doors
- All chambers are fabricated in the USA, using materials also produced in the USA
Gas Quenching System
- The high performance, external gas quench system provides the lowest resistance, highest efficiency gas flow in the industry for rapid cooling at pressures up to 2 bar (15 PSIG). An appropriately sized motor drives a computer balanced, radial bladed fan to recirculate the quench gas straight through the water-to-gas heat exchanger and then into the hot zone at high velocity. The unique tapered graphite gas nozzles are positioned to direct quench gas at the work load for optimum cooling. Up to 3 equally sized gas cooling systems will provide for uniform cooling of the furnace.
- If in the unlikely event it is ever necessary to access or remove the heat exchanger or quench motor or fan wheel, all components can be easily serviced through the appropriate end plates of the separate, external housing.
Vacuum Pumping System
- Mechanical Pump: Edwards Stokes Microvac rotary piston
- Booster Blower: Edwards Stokes direct drive
- Diffusion Pump: Varian/Agilent
- Holding Pump: Alcatel
- High Vacuum Valve: Pneumatically operated, right angle poppet valve
*other pumping configurations are available
Control Cabinet and Instrumentation
At the heart of the furnace control system is the SolarVac® controls and automation. This advanced control system is capable of vacuum furnace control and monitoring even while at a remote location.
- All industrial controls and instrumentation are housed in a suitable NEMA 12 control cabinet.
- Cabinet is designed to NFPA Standards and electrostatically powder coated to match the furnace system.
- Operator Interface: High Definition touchscreen 21.5” “Human Machine Interface”
- Programmable Logic Controller: Allen-Bradley CompactLogix
- Over-temperature Controller: Honeywell Model UDC2500
- Graphic Recorder: Eurotherm 6100 Series with up to 48 input channels and Ethernet capabilities
- Vacuum Gauge Controller: Televac
- Control and over-temperature Thermocouples: Type “S” with additional SAT ports available
- Work Thermocouples: Type “K” or type “N”, built in guaranteed soak feature
Equipment and Energy Savings Options
- ConserVac® energy-saving control system
- ElementGuard off-line heating element protection system
- Variable Frequency Drives (VFD) or soft-start motor starters are available in place of across-the-line motor starters for optimum quench motor performance.
- Gas backfill reservoir
- Recirculating water cooling system
- Carbon Fiber, high temperature alloy and molybdenum work grids
*Additional options are available upon request.
HCB Series Standard Furnace Sizes
Work Zone Size (WxHxD) | Load Capacity | |
HCB-84 | 54″ x 54″ x 144″ (12 feet) | 50,000 lbs |
54″ x 54″ x 288″ (24 feet) | 100,000 lbs | |
54″ x 54″ x 432″ (36 feet) | 150,000 lbs | |
54″ x 54″ x 576″ (48 feet) | 150,000 lbs | |
HCB-120 | 80″ x 80″ x 432″ (36 feet) | 150,000 lbs |
*Other sizes available as required
Typical Materials Processed in Horizontal Car Bottom Loading Vacuum Furnaces
- Alloy Steels
- Titanium
- Tantalum
- Inconel
- Nitinol
- Stainless Steel
- Tool Steel
- Precipitation Hardening Stainless Steel (PH)
- AerMet® 100
- Tungsten
- Zirconium
- High Speed Tool Steels
- Copper
- Brass
- Hot Working Tool Steels
- Nickel Based Alloys
- . . . and more
Typical Components Processed in Horizontal Car Bottom Loading Vacuum Furnaces
- Aircraft parts and equipment
- Power Generation blades and components
- Medical devices
- Additive Manufactured components
- Implants
- Tooling
- Gears
- Braze assemblies
- Plate
- Forgings
- Bar
- Ingots
- Weldments
- Structural components
- Castings
- Sheet
- Tube and pipe
- . . . and more