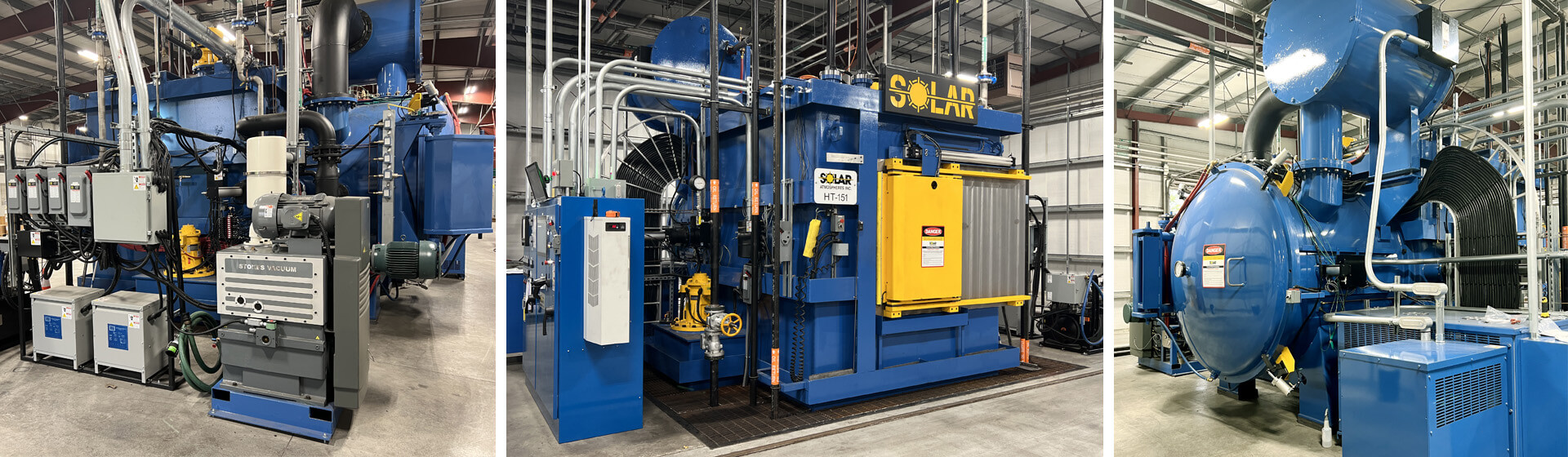
NEO™ – Vacuum Oil Quench Furnace
Vacuum Oil Quench Furnace
Safe, Green, Economical Furnace
The NEO™ Vacuum Oil Quench Furnace is a batch-type graphite insulated furnace designed to accommodate medium-sized workloads in an efficient, environmentally friendly, and economical manner. The main feature of the furnace is its ability to SAFELY and ENVIRONMENTALLY heat treat and oil quench workloads of alloys that require cooling rates that exceed high-pressure gas quenching’s practical capabilities.
Features and Benefits
Safety
- No open flames / no flame curtains
- No direct water cooling of oil, no risk of water oil mixing and fire hazard
- No endo gas burn-off
- Load transfer is innovative, smooth, hydraulically operated
Environmentally Green
- Zero Combustion for atmosphere control, therefore no COx and NOx effluents
Metallurgical
- Neutral vacuum atmosphere; can group different alloys in one batch
- No oxygen probes
- No decarb / carburization
- No intergranular oxidation
- Cleaner surface finish on parts
- Gas cool or oil quench
- Can use thermocouples for actual work temperature measurement during heating and soaking
Economical
- Graphite insulated energy efficient electrically heated hot zone
NEO™ – Specifications
Hot Zone
- Work Zone: 36″W x 36″H x 48″D
- Operating temperature: 2100°F
- Maximum temperature: 2200°F
- Temperature uniformity: ±10°F
- AMS 2750 compliant
- Survey temp points at 1000°F / 1500°F / 2100°F
- Insulation: 2.0″ thick HEFVAC graphite board
- Heating Elements: straight, segmented graphite elements
- Hearth: 2,000 pound capacity; TZM molybdenum work support pins, graphite hearth rails
- Support Structure: Insulation and heating elements mounted on a heavy duty 0.090″ thick stainless steel fabrication
Power Supply
- Magnetic Specialties SCR power supply rated at 180 kVA
Vacuum Chamber
The heating chamber is a double-walled, water cooled, horizontal loading vacuum chamber. An O-ring sealed rear door with pneumatic clamps allows for safe access of personnel for maintenance, adding work thermocouples to the load, and installation of temperature uniformity survey racks. Pneumatically operated sliding front door for loading and unloading workloads. Oversized water inlets and outlets allow maximum cooling water recirculation flow. Painted inner heating chamber wall minimizes build-up of contaminates and provides an easy to clean surface.
Gas Cooling System
The internal gas cooling system includes a 30 HP motor which drives a high-speed centrifugal fan to recirculate the quench gas straight through the gas-to-liquid heat exchanger and then into the hot zone. The gas cooling is performed at a pressure of -5″ Hg and may be used to cool parts that require lower cooling rates for metallurgical purposes however is primarily used to cool the hot zone down as needed for re-loading or maintenance purposes.
Oil Quenching System
The oil quenching system includes the loading and unloading hydraulic, linearly actuated, chain driven, mechanism and a 3,000-gallon vacuum-rated oil tank. Automatic or manual closed loop position and speed control for workload motion. Dual 10 HP impellers with variable frequency drives are used to circulate the oil across the parts during the quenching process. Alternatively, the parts can be quenched without oil circulation.
Vacuum Pumping System
- Mechanical Pump: Stokes 412J, high capacity 300 CFM vacuum piston pump
- Vacuum Booster Pump: Stokes 615, 1300 CFM booster pump
- Process Gas System: Backfill, partial pressure and pneumatics with Nitrogen gas
Control and Automation Instrumentation
The SolarVac® Polaris is a PLC based control system with operator interface, recipe storage, alarm management, and data acquisition functions. Enables the operator to monitor, control, record, and quickly understand the status of the furnace operation. Includes Historian data acquisition and connectivity for the benefit of preventive maintenance, quality management, and production metrics. All controls and automation are housed in a suitable NEMA 12 control cabinet.
- HMI Operator Interface: Industrial PC with Intel i5 CPU and Windows 10; Wonderware InTouch supervisory-level HMI software package; 21.5ʺ HD color touchscreen monitor.
- Programmable Logic Controller: Allen-Bradley CompactLogix
- Furnace Temperature Controller: Honeywell Model UDC 3500
- Over-temperature Controller: Honeywell Model UDC 2500
- Graphic Video Recorder: Eurotherm Model 6180A, with 48 channels and a 12ʺ color touch screen display
- Vacuum Measurement and Recording using Active Gauges including capacitance monometers and convection gauges
- Control and Over-temperature Thermocouples: Type “S”
- Work Thermocouples: Type “K”
- Low energy element ground protection system
- Remote access
- Option for Low Pressure Carburizing (LPC) capabilities
Additional Information
All Solar Manufacturing furnaces and replacement hot zones are designed for long life, easy maintenance, minimal downtime, and low cost of operation. Not only is each furnace fully tested prior to shipment, a Factory Service Engineer starts-up and field tests after installation. Every Solar Manufacturing furnace and hot zone carries a full one (1) year warranty.